BIFIN & MONOFIN
EXPLORE OUR FIN COLLECTION
BLADE WITH 3K SURFACE
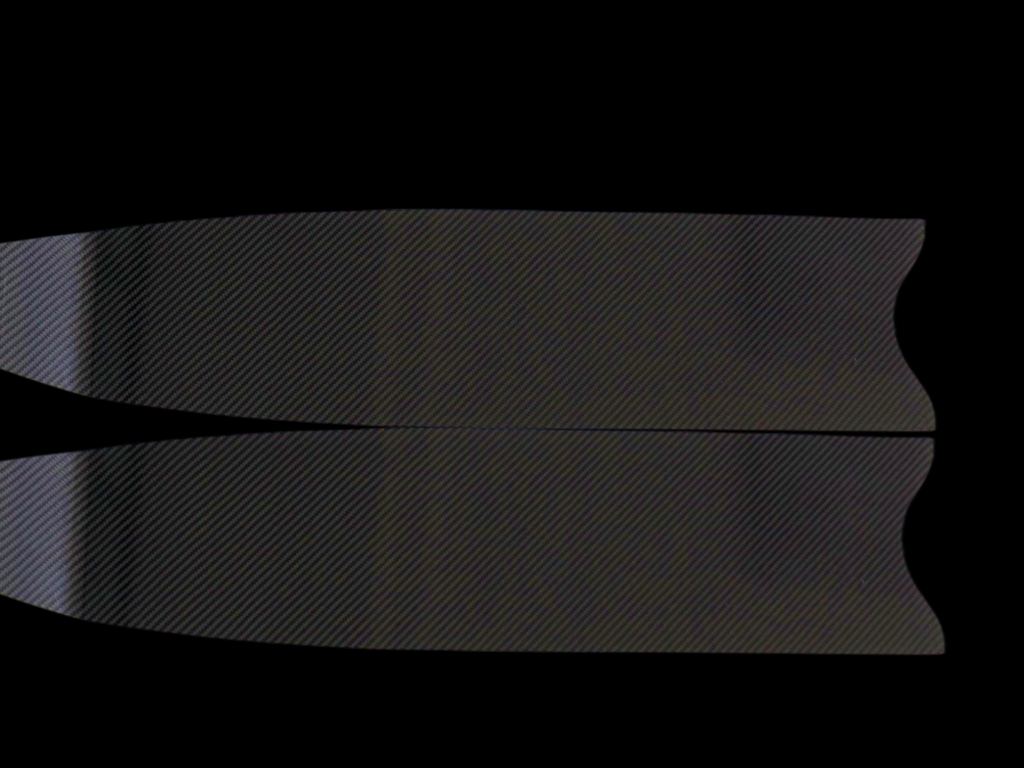
BLADE WITH 20*20 FRAME

BLADE WITH CUBIC FRAME
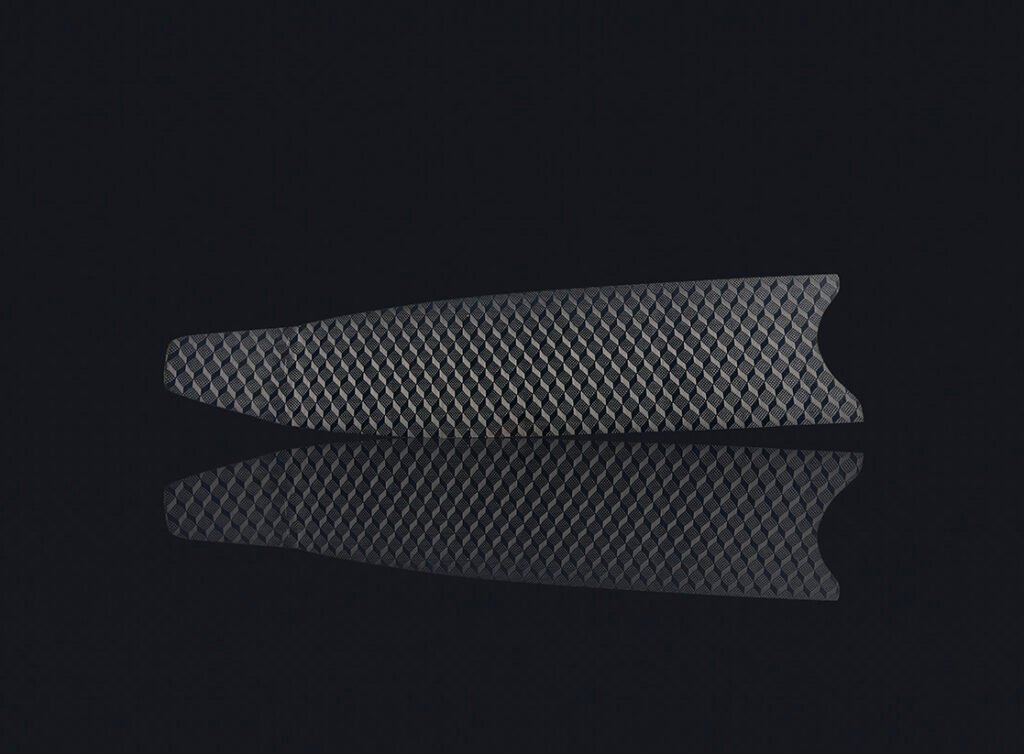
BLADE WITH CAMO
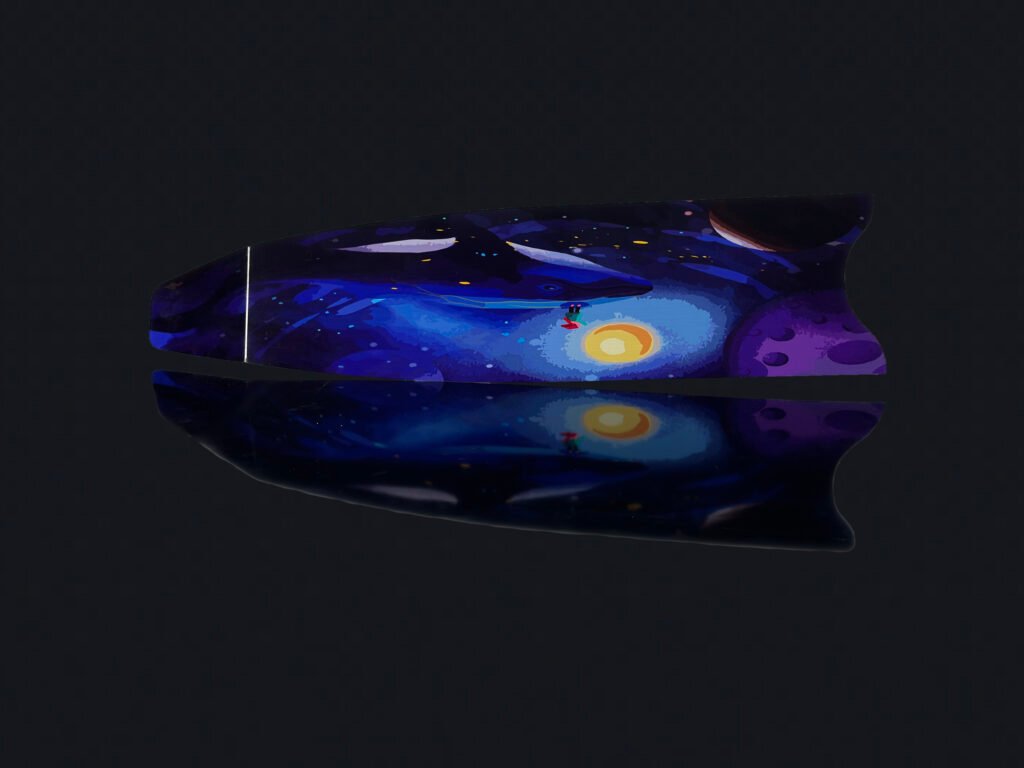
PRODUCTION PROCESS
IT'S ALL ABOUT QUALITY AND TECHNOLOGY
Autoclaving enhances fins production by improving efficiency, meeting deadlines, and ensuring superior quality through precise control of the manufacturing process.
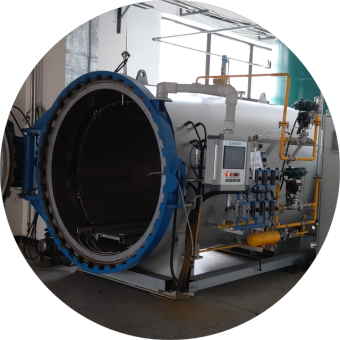
HELP CENTER
MORE ABOUT AUTOCLAVING
The autoclaving process for fin production presents several advantages:
High-Quality Cure: Autoclaving applies both heat and high pressure evenly across the material, leading to a superior cure of the resin. This results in fins that have improved mechanical properties, such as increased strength and stiffness.
Void Reduction: The high pressure helps to reduce voids within the composite material. Voids are small air bubbles that can form within the resin and weaken the structure. The pressure in an autoclave ensures that these voids are minimized, leading to a denser, more uniform material.
Better Fiber Consolidation: Autoclaving enhances the consolidation of the fibers, ensuring that the resin thoroughly impregnates the carbon or fiberglass material. This ensures that the fibers are fully bonded and optimizes the strength-to-weight ratio of the fins.
Controlled Environment: The autoclave process is conducted in a controlled environment, which allows for precise control over temperature and pressure throughout the cure cycle. This control is crucial for achieving consistent results in the production of high-performance fins.
Improved Surface Finish: Fins produced in an autoclave tend to have a smoother and more aesthetically pleasing surface finish. This is because the pressure compacts the material and reduces surface irregularities.
Durability: The combination of heat, pressure, and a controlled environment leads to fins that are not only strong and lightweight but also more durable and resistant to fatigue and environmental effects like UV exposure and saltwater corrosion.
QUALITY CONTROLL
The production of carbon fiber fins effectively controls quality through meticulous oversight of both raw materials and the manufacturing process. Starting with the selection of premium materials, such as fabric sourced from Japan’s Toray Industries, known for producing high-quality carbon fiber, the emphasis is on using top-tier components.
In the manufacturing process, precision plays a pivotal role. Techniques like layering, molding, and, crucially, autoclaving are employed. Autoclaving subjects the fins to controlled temperature and pressure, ensuring thorough curing and bonding of the carbon fiber layers. This process contributes to the creation of a consistent, high-strength structure, a hallmark of quality carbon fiber fins.
Quality control is integrated throughout production. Skilled technicians closely monitor each phase, identifying and addressing any potential deviations from specifications. Rigorous testing procedures, including stress tests and structural analyses, are applied to assess the fins’ performance and durability.
The use of advanced technology and automation in the manufacturing process further enhances quality control. Automated systems help maintain consistency and precision, reducing the likelihood of defects. Additionally, final products undergo thorough inspections to confirm compliance with design specifications and quality standards.
HOW DO MATERIALS AFFECT THE STRENGTH AND WEIGHT OF FINS, SUCH AS FIBERGLASS AND CARBON?
The production of carbon fiber fins effectively controls quality through meticulous oversight of both raw materials and the manufacturing process. Starting with the selection of premium materials, such as fabric sourced from Japan’s Toray Industries, known for producing high-quality carbon fiber, the emphasis is on using top-tier components.
In the manufacturing process, precision plays a pivotal role. Techniques like layering, molding, and, crucially, autoclaving are employed. Autoclaving subjects the fins to controlled temperature and pressure, ensuring thorough curing and bonding of the carbon fiber layers. This process contributes to the creation of a consistent, high-strength structure, a hallmark of quality carbon fiber fins.
Quality control is integrated throughout production. Skilled technicians closely monitor each phase, identifying and addressing any potential deviations from specifications. Rigorous testing procedures, including stress tests and structural analyses, are applied to assess the fins’ performance and durability.
The use of advanced technology and automation in the manufacturing process further enhances quality control. Automated systems help maintain consistency and precision, reducing the likelihood of defects. Additionally, final products undergo thorough inspections to confirm compliance with design specifications and quality standards.
POPULAR QUESTIONS
Yes, you can have your blades customized to any sizes. No limitation on the angle and shapes. Drop us a message and we will make it come true.
In the official order, the MOQ for each hardness is 50 pairs. It’s OK for us to start with trial orders.
It depends on the order quantity and the number of molds for making blades. The daily output is 240-360pcs.
All parts are guaranteed FREE from manufacturer defects for 1 year.
Silicone and EPDM.
Yes, you can have the side rails customized to the shape and color you like.
50% deposit before production and 50% balance before the shipment.
REVIEWS
CUSTOMER REVIEWS
Valerie,
We are very happy about the quality of the blades!
I will assemble them on footpockets and send for real conditions testing.
I will let you know the feedback later.
But when I take it in hand and compare to our medium, the stiffness seems very close indeed.
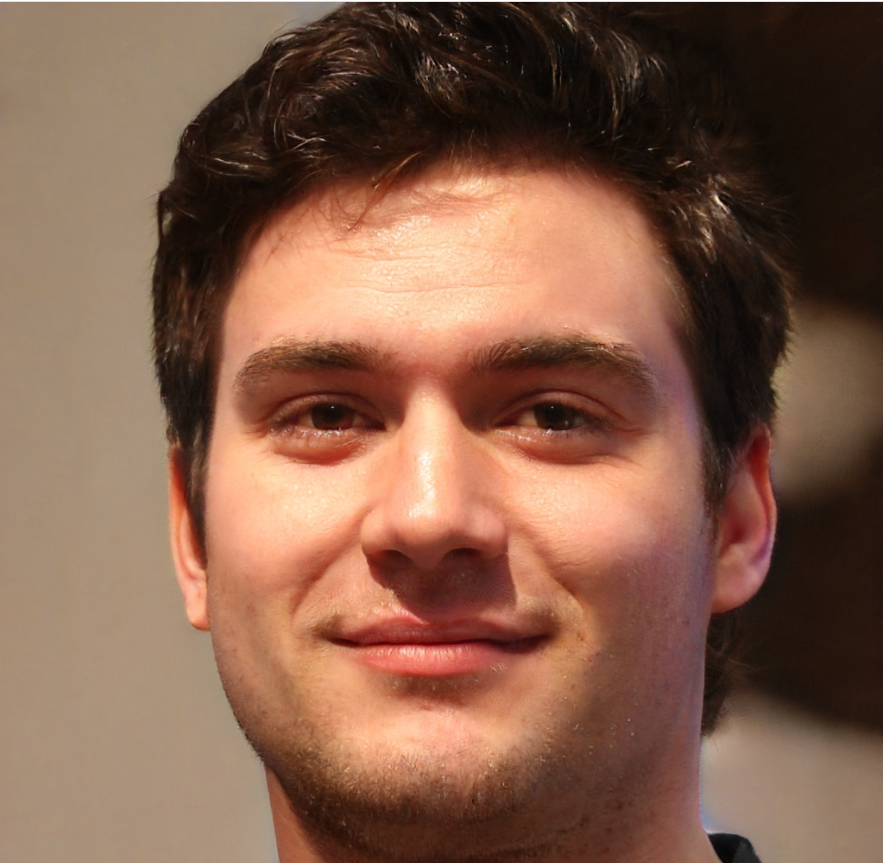
Hi Valerie,
Well received the blades with thanks.
Firstly feeling, the quality is matching with our expectations.
The side rail gluing is clean. Good Job.
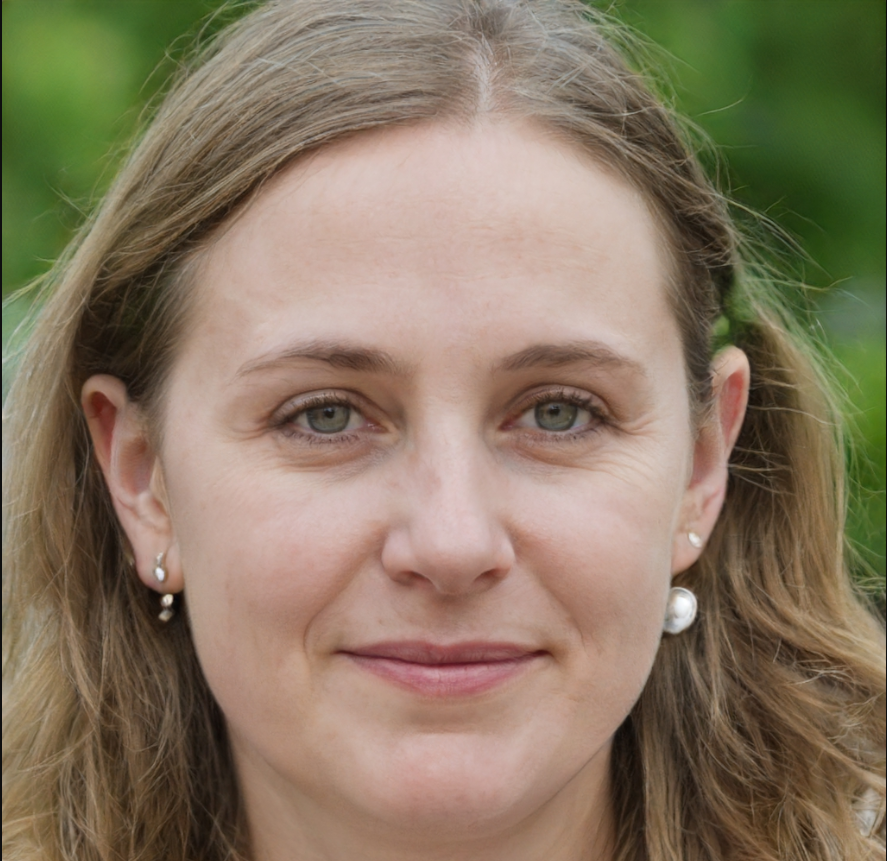
Dear Valerie,
Because of your product is very interesting for us.
Could you make some golden samples, including our water rails ( in order to verify the gluing process ), printed logo and sticker with ” made in ” and serial number? We need to evaluate your different thickness too.
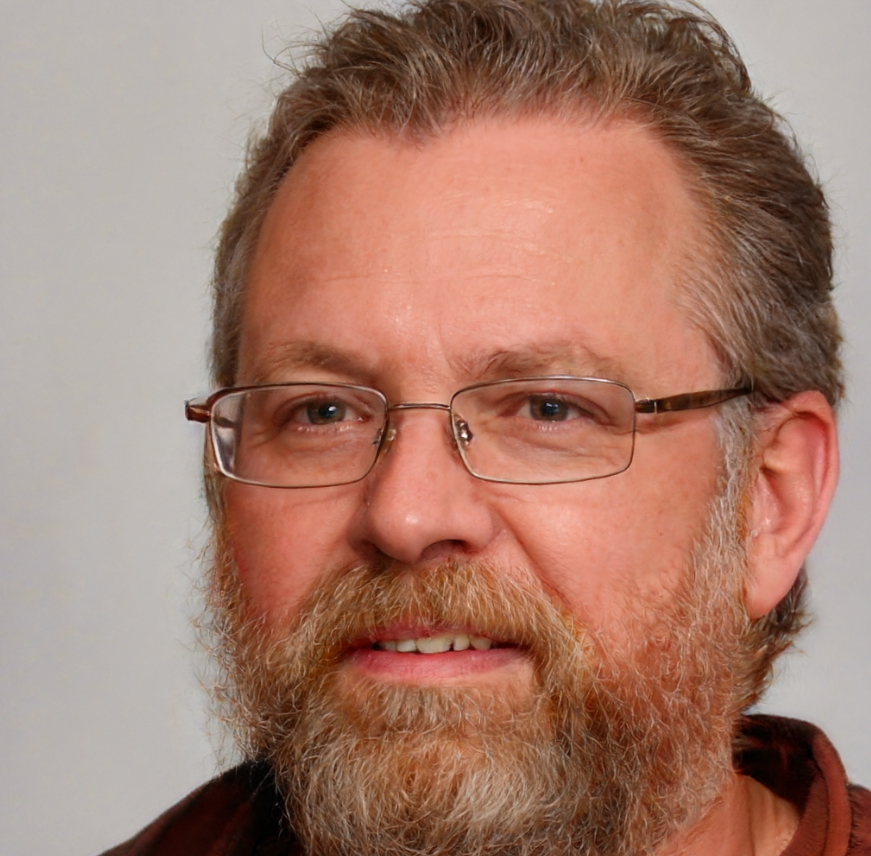
Hi Valerie,
Yes, we well received them, sorry for the late reply.
My colleague who’s responsible for the fins development is really impressed of the blades quality. As well as me for the carbon tube.
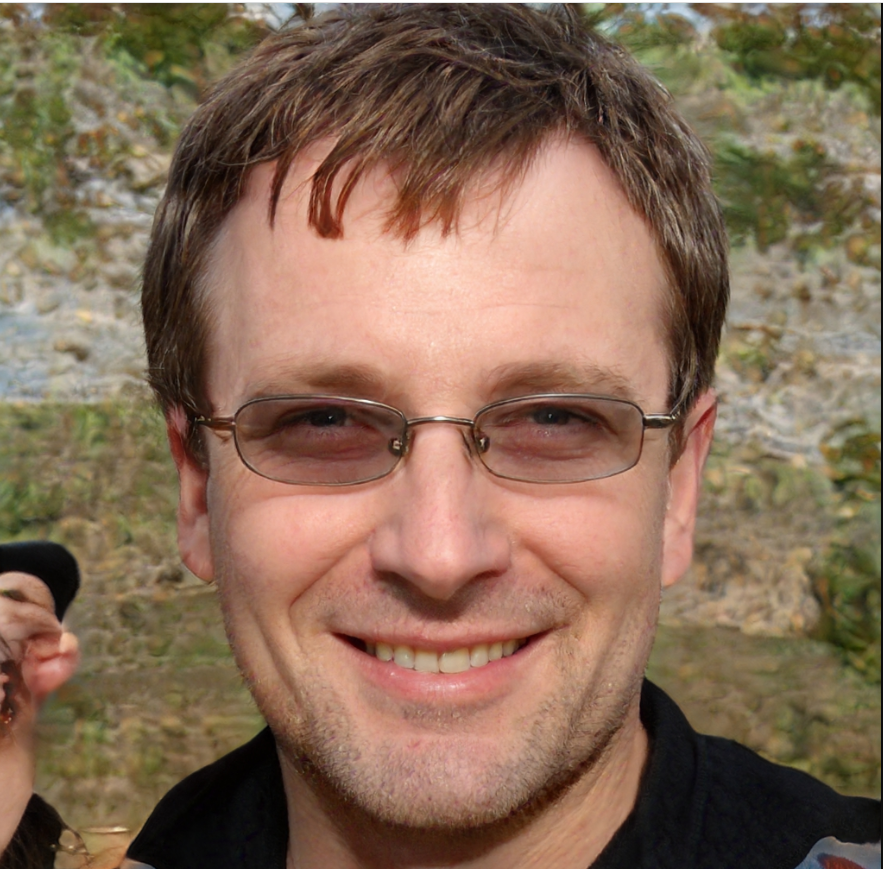